Understanding CNC Lathing Parts and Their Impact on Metal Fabrication
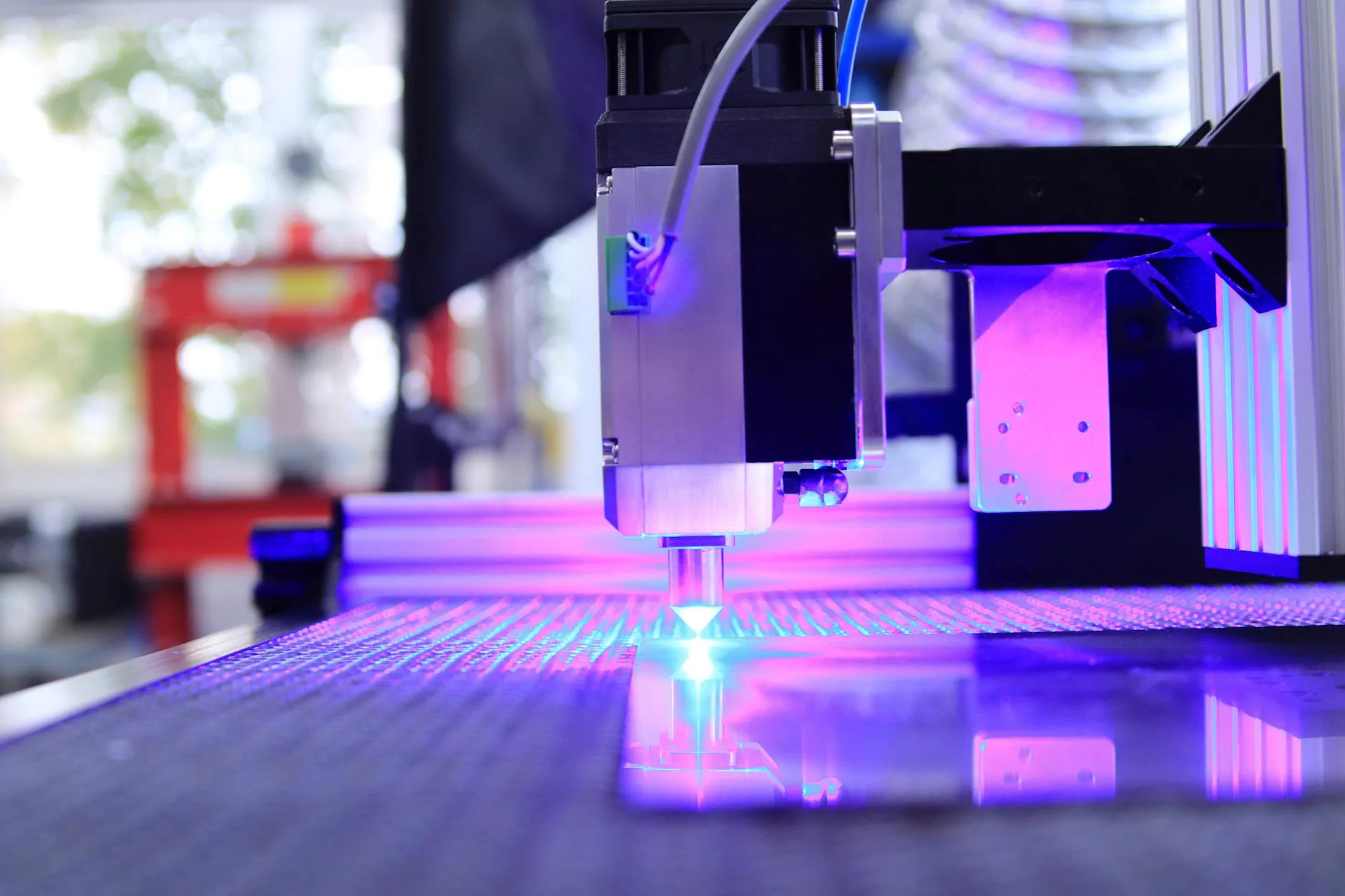
CNC lathing parts have become a cornerstone in the world of metal fabrication, largely due to their capacity for achieving precise dimensions and complex designs. As industries continue to evolve, the demand for accuracy, efficiency, and customization increases, making the relevance of CNC (Computer Numerical Control) technology more pronounced. This article delves into the significance of CNC lathing parts, how they revolutionize manufacturing processes, and why businesses in the metal fabrication sector must embrace this transformative technology.
What are CNC Lathing Parts?
CNC lathing parts refer to components produced using a CNC lathe, a machine that executes precise rotational movements to shape materials like metals and plastics. This technique allows for the creation of various parts including shafts, housings, and other intricate components that are essential in a wide range of applications.
Unlike traditional lathes, CNC lathes are computer-controlled, meaning that they can execute programmed movements with remarkable accuracy. This level of control not only enhances part quality but also increases production speed, setting it apart as a preferred method in modern manufacturing.
The Advantages of CNC Lathing Parts in Metal Fabrication
The transition from conventional manual processes to CNC lathing in metal fabrication bears numerous advantages:
- Precision: CNC lathing ensures an unmatched level of precision, crucial for applications where tolerances are critical.
- Automation: Automated processes reduce human error, allowing for consistent product quality across lots.
- Complex Designs: CNC technology enables the creation of complex and intricate part designs that were previously unattainable with manual methods.
- Efficiency: Increased production rates lead to shorter lead times, which can be a game changer in meeting market demands.
- Cost-Effectiveness: While initial investments may be higher, the reduction in labor and material waste makes CNC lathing a cost-effective choice in the long run.
Applications of CNC Lathing Parts
CNC lathing parts find applications across a diverse array of industries, including but not limited to:
- Aerospace: High-stakes aerospace components that require exact specifications.
- Automotive: Parts production for vehicles, including shafts, gears, and engine components.
- Medical Devices: Precision components for medical tools and devices that uphold safety standards.
- Industrial Machinery: Production of essential machinery parts that enhance productivity in various sectors.
- Consumer Products: Custom parts for household items and technology gadgets.
How CNC Lathing Parts are Manufactured
The manufacturing process of cnc lathing parts involves several critical steps designed to ensure quality and accuracy:
- Design Creation: It all starts with a detailed design, often facilitated by CAD (Computer-Aided Design) software that enables designers to create precise 2D and 3D models.
- Programming: The design files are then converted into a code that can be read by the CNC machine, typically in G-code format.
- Machine Setup: Operators set up the CNC lathe, installing the required tooling and fixtures to hold the material securely.
- Machining: The CNC machine executes the programmed instructions, rotating the material while progressively cutting it into the desired shape.
- Quality Control: After machining, the parts undergo rigorous inspection to ensure they meet specifications and tolerances. This may involve various methods such as CNC coordinate measuring machines (CMM) or laser scanning.
Quality Assurance in CNC Lathing Parts Production
Quality assurance is paramount in the production of cnc lathing parts. Companies must integrate quality checks at multiple stages of the manufacturing process. Here are some best practices:
- Material Inspection: Every batch of raw material should be inspected for compliance with industry standards.
- Process Monitoring: Constant monitoring during the machining process to detect anomalies.
- Final Inspection: Conduct a comprehensive evaluation of the final product to ensure all specifications are met.
- Documentation: Maintain detailed records of inspections performed and any corrective actions taken.
Choosing the Right CNC Lathing Service Provider
Finding a proficient provider for cnc lathing parts production is critical for achieving project success. Here are some tips to guide your selection:
- Experience: Look for a company with solid experience in CNC machining, particularly in your industry.
- Capabilities: Ensure they have the necessary machinery and technology to meet your specifications.
- Reputation: Research their track record through online reviews and testimonials from previous clients.
- Certifications: Check for industry-related certifications which indicate a commitment to quality.
- Customer Support: Evaluate their customer service and communication practices to ensure a smooth project flow.
The Future of CNC Lathing Parts
As technology advances, the future of cnc lathing parts holds exciting prospects. Innovations such as additive manufacturing and enhanced automation are expected to revolutionize the industry further. The integration of artificial intelligence (AI) into CNC machining could lead to smarter and more adaptive manufacturing processes, significantly enhancing efficiency and reducing downtime.
Conclusion
In conclusion, cnc lathing parts represent a significant advancement within the realm of metal fabrication, offering transformative benefits in precision, efficiency, and versatility. As global industries continue to seek solutions that meet increasingly complex demands, embracing CNC technology and its capabilities will be a vital factor in maintaining a competitive edge.
For those in the metal fabrication industry looking to augment their production capabilities, the expertise and technology offered by manufacturers specializing in CNC lathing parts, such as Deepmould.net, are indispensable. By integrating these advanced manufacturing processes, companies are better equipped to innovate and thrive in a rapidly evolving marketplace.